The hydraulic hose mainly consists of four parts. The most important requirement of the standard hose is to have a strong connection and excellent sealing effect to ensure its normal working function. If it is unsuccessful, we will start with the appearance and internal structure, and analyze the reasons why it cannot be used. Generally speaking, in addition to oil leakage in the buckling direction, there are three reasons for hydraulic transition joint manufacturers.
1. Bursting pipe body. According to the burst direction, pipeline burst can be divided into two ways. First, the bursting direction is located on both sides of the hose, within 25mm of the flexural grommet. The reason for the bursting in this direction is the improper manufacture or installation of the rubber tube, such as the rubber tube being stretched and twisted together during the installation and use process, maybe the roughness of the rubber tube is lower than the minimum allowable roughness. Second, the ripping spacing button coat 25mm. Most of the reasons for this type of burst are excessive working pressure of the hydraulic press management system or damage to the pipe body.
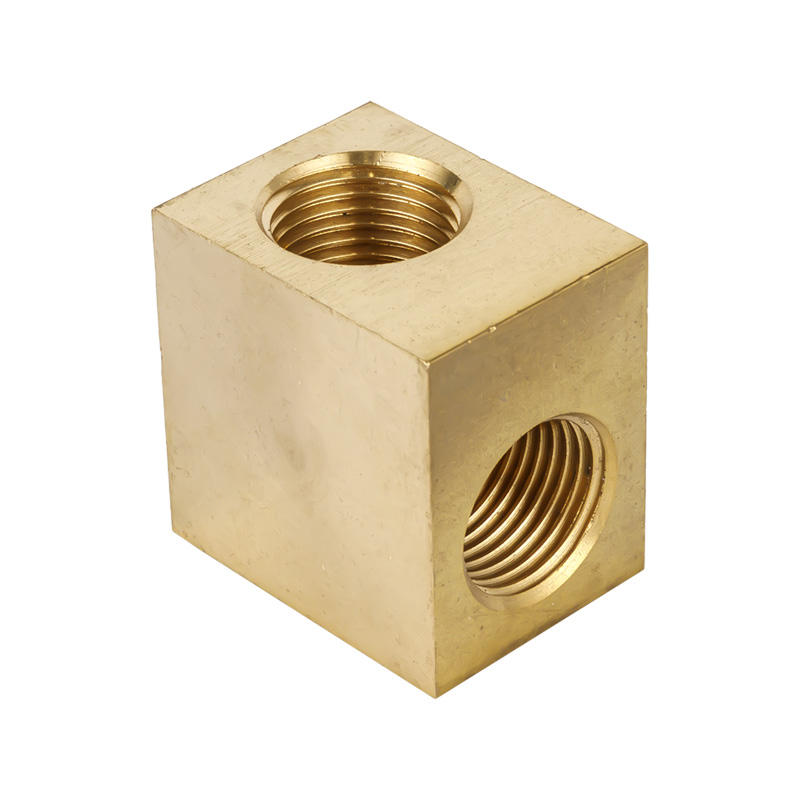
2. Oil leakage from sand holes on the body of the hydraulic hose. The oil leakage of the trachoma in the pipe body of the custom hydraulic joint manufacturer is generally reflected in the oil leakage or linear introduction after the vulcanized rubber bubble outside the hose. The blisters on the tube body are mainly caused by the product quality problems of the rubber tube, such as the residue in the super glue in the tube body. Part of the tube body is damaged. The problem of the tube body when the mold is ejected, etc.
3. Oil leakage at the joint. The oil leakage at the joint is mainly due to the inconsistency of the dimensional accuracy of the vulcanized rubber hose connector and the butt joint to other components, perhaps because of the mismatch between the vulcanized rubber hose connector and the over-connector. We should not panic if hydraulic hoses exhibit common failures. The first analysis of the existing problem is that the pipe body has burst, and the ferrule type straight-through pipe joint or some butt joints have oil leakage. After grasping the cause of the problem, it may be possible to replace the connector or pipeline with the matching dimensional accuracy. , to ensure that it is not easy to endanger subsequent manufacturing.